Which automatic bagging machine is right for your production?
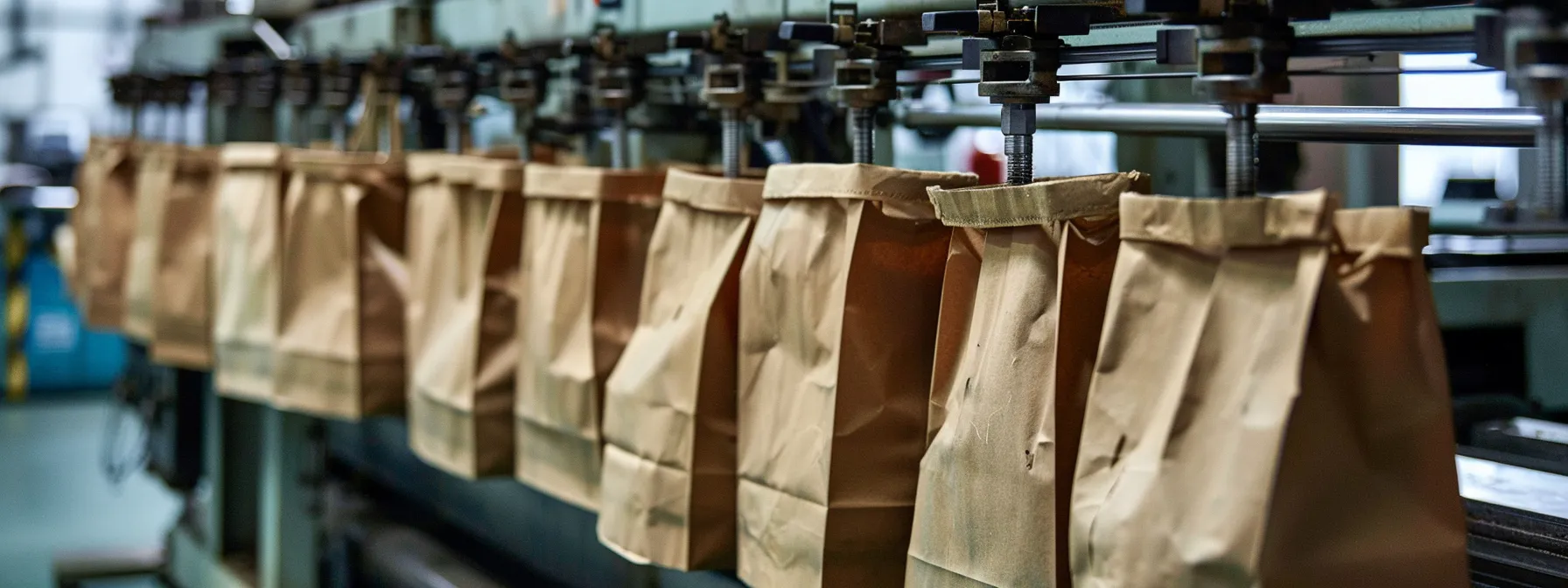
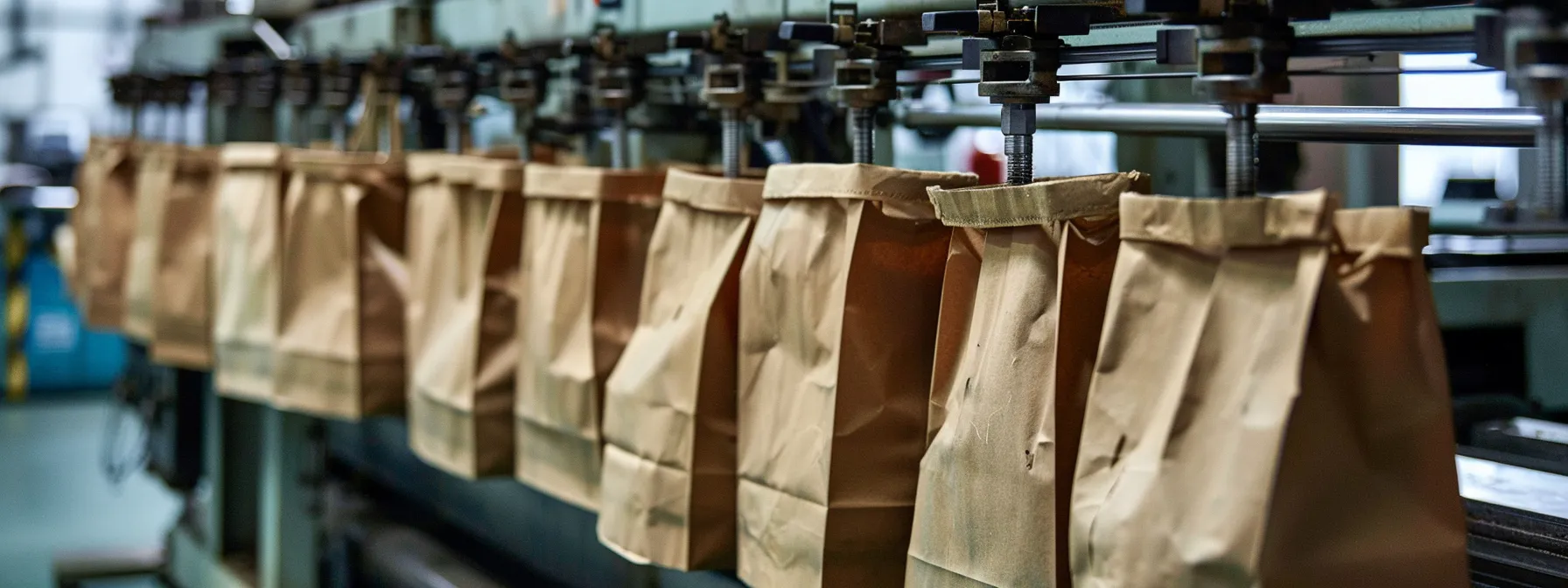
Choosing the Right Automatic Bagging Machine for Your Production Needs
Selecting the right automatic bagging machine can significantly impact your production efficiency. This guide will explore key factors to consider when choosing a bagging machine, including machine types, production capacity, and maintenance requirements. By understanding these elements, you’ll be better equipped to make an informed decision that aligns with your business needs and enhances your packaging process. Let’s dive into the world of automatic bagging machines and find the perfect fit for your production line.
Understanding automatic bagging machines and their functions
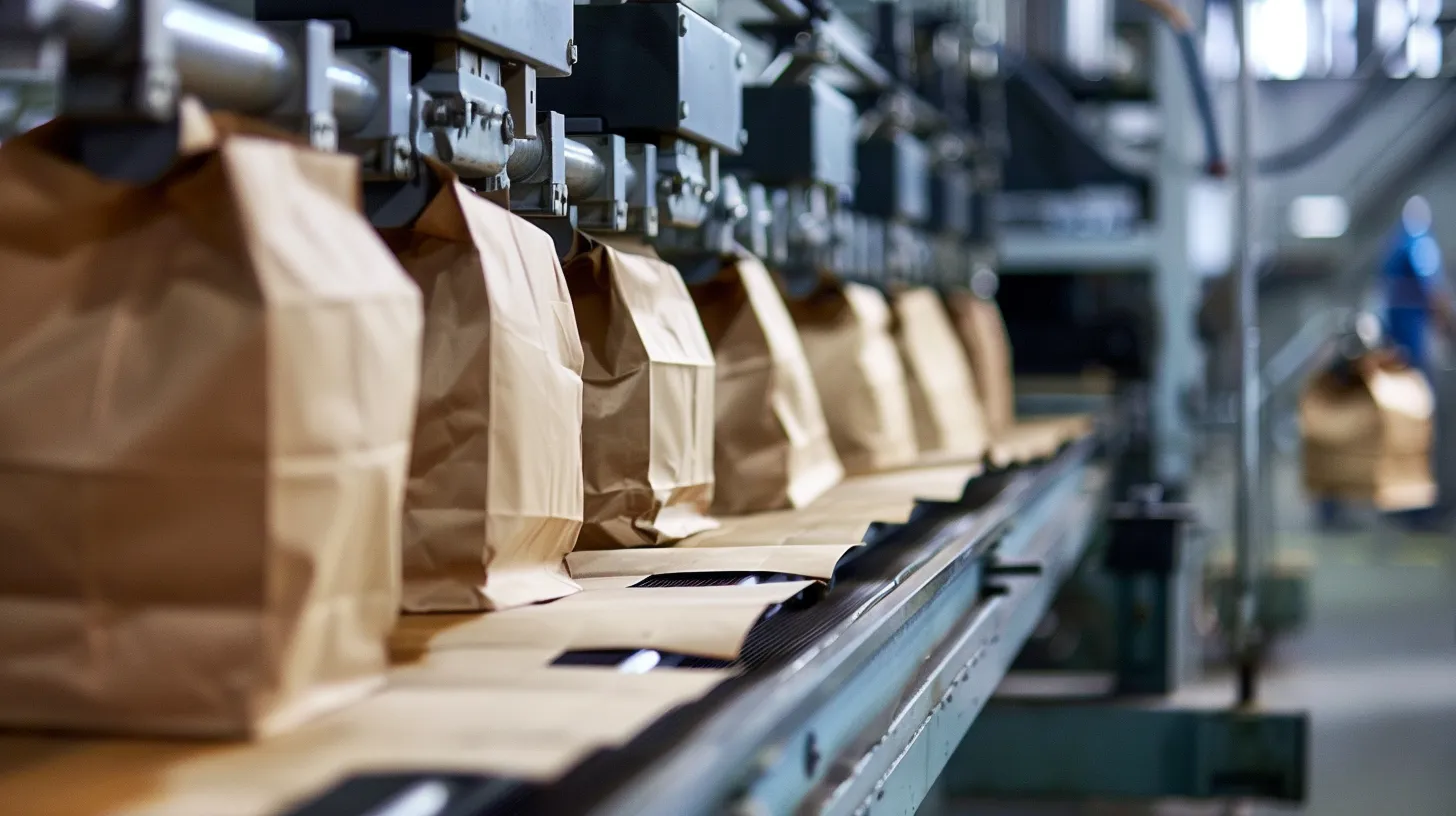
Automatic bagging machines streamline packaging processes in various industries. These efficient baggers handle products ranging from powders to cement to food materials, adapting to customer needs. Feedback from users highlights their versatility and energy efficiency, with some models operating on as little as 500 watts.
The core functions of automatic bagging machines include:
- Product weighing and dispensing
- Bag opening and filling
- Sealing and labeling
- Discharge of filled bags
Selecting the right bagger depends on production volume, product characteristics, and packaging requirements. Manufacturers offer customized solutions, incorporating features like dust extraction for powders or gentle handling for delicate items. Regular maintenance ensures optimal performance and longevity of these essential packaging tools.
Key factors to consider when selecting an automatic bagging machine
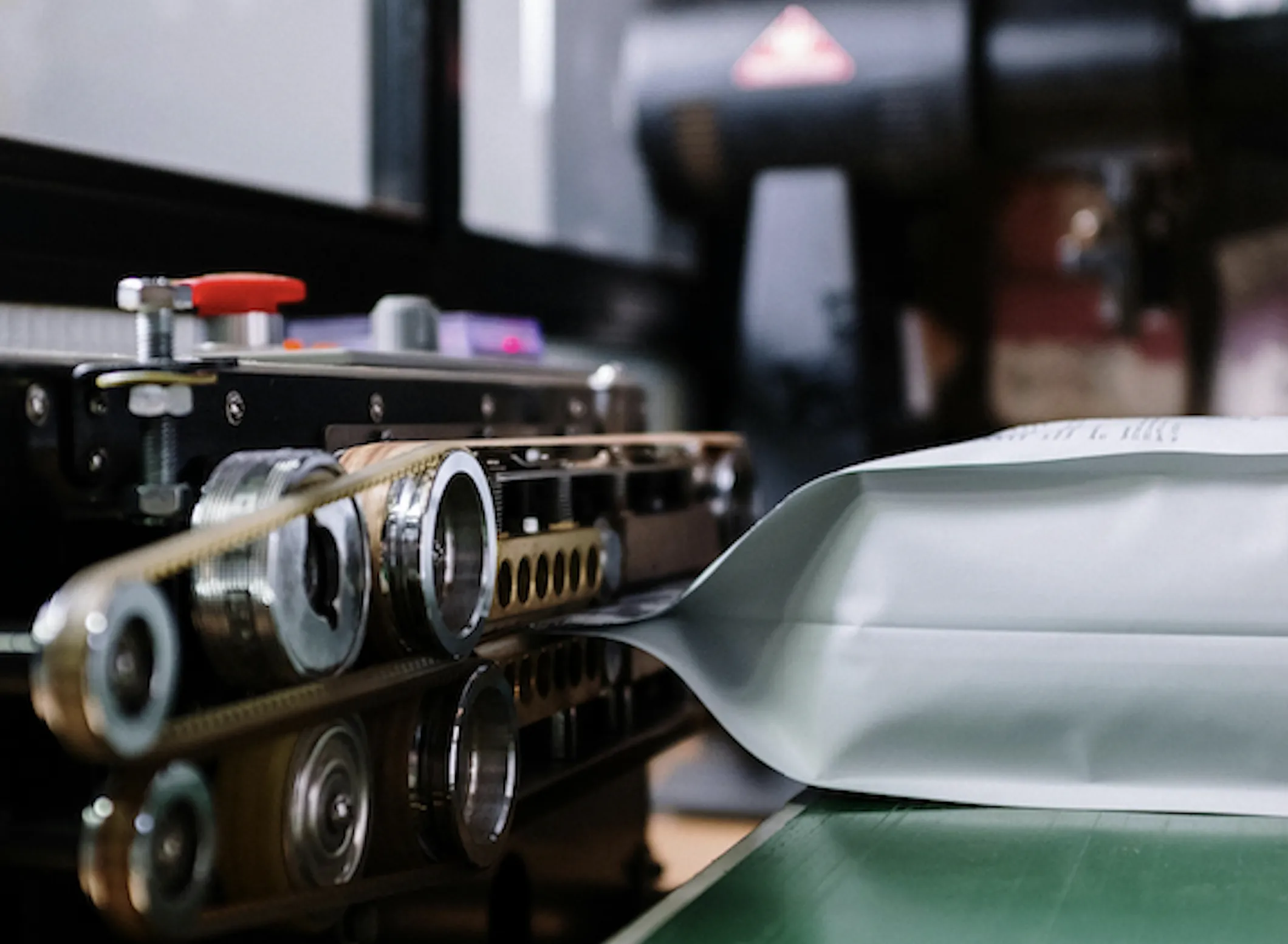
Selecting an automatic bagging machine requires careful consideration of production volume, speed requirements, bag types, and automation levels. Understanding the architecture of these machines helps businesses choose systems that align with their needs and transport capabilities. Here are some key factors to evaluate to ensure the selected machine enhances operational efficiency and supports brand objectives.
Assessing your production volume and speed requirements
Evaluating production volume and speed requirements is crucial for selecting an appropriate automatic bagging machine. High-volume operations in the food industry may require machines capable of handling multiple reels simultaneously, while smaller consumer goods producers might opt for single-reel systems. The machine’s speed directly impacts output and cost efficiency, with faster systems generally commanding higher prices but potentially offering greater long-term value through increased productivity and reduced labor costs. Companies must also consider the weight and dimensions of their products to ensure the chosen machine can accommodate their specific packaging needs.
Evaluating different bag types for your products
Selecting the appropriate bag type is crucial for the optimal performance of automatic bagging machines. Manufacturers must consider factors such as seal strength, machine footprint, and product characteristics. For example, companies in France may prefer specific bag styles that align with local packaging norms. The machine’s language interface and compatibility with various carton sizes also influence the selection process. Key considerations include:
- Material compatibility with the product
- Seal type and strength requirements
- Machine footprint and available floor space
- Compatibility with existing carton sizes
- Language options for machine interface
Analyzing automation levels needed for your operations
Determining the appropriate automation level for automatic bagging machines is crucial for industries like chemical manufacturing and beverage production. Companies must assess their current production needs and future growth projections to select a system that offers the right balance of efficiency and flexibility. For instance, a nylon bag manufacturer might require a highly automated system capable of handling woven fabrics, while a drink packaging company may need a machine that can accommodate various bag sizes and materials. The chosen automation level should align with the company’s operational goals, workforce capabilities, and budget constraints:
The benefits of efficient packaging machines

Efficient packaging machines offer businesses significant benefits, from enhancing throughput to reducing labor costs. These systems improve packaging consistency and quality, which are crucial for industries like agriculture. Environmental impact is also addressed through efficient solutions. Companies can expect increased productivity, with some machines processing thousands of bags per hour.
Enhancing throughput and reducing labor costs
Automatic bagging machines significantly enhance throughput and reduce labor costs in production facilities. By automating the filling station process, these machines efficiently handle various materials, including polyethylene products, minimizing waste and maximizing output. The advanced capabilities provide real-time information on production metrics, enabling managers to optimize operations and allocate resources effectively. Companies implementing these systems often experience substantial improvements in efficiency and cost-effectiveness:
- Increased production speed and consistency
- Reduced manual labor requirements
- Improved accuracy in product weighing and filling
- Minimized material waste through precise dispensing
- Enhanced data collection for process optimization
Improving packaging consistency and quality
Automatic bagging machines significantly improve packaging consistency and quality across various industries. These machines precisely measure and dispense materials, whether it’s soil for plant nurseries or biodegradable plastic for eco-friendly packaging, ensuring uniform bag weights and sizes. By utilizing gravity-fed systems and advanced sensors, they maintain consistent fill levels and reduce human error, resulting in professional-looking packages that meet industry standards.
Environmental impact of efficient packaging solutions
Efficient packaging solutions, including paper bag making machines, significantly reduce environmental impact through innovative design and data-driven optimization. These machines minimize waste by precisely measuring materials and utilizing eco-friendly options like paper or biodegradable plastics. Advanced learning algorithms in modern bagging systems continuously improve efficiency, reducing energy consumption and carbon footprint. Concrete examples of environmental benefits include:
Different types of bagging machines available

At Newlong, we specialize in high-quality packaging machinery, offering a wide range of solutions for bag-making, bag closing, and automated bagging systems. Our lineup includes the NP-7A portable bag closer, the DS-9C high-speed sewing machine, and the FA series fully automated bag closing systems. For bag production, we provide tubing machines like the CT-10 and bottoming machines such as the BT-11, designed for multi-wall paper bags used in industries like cement, food, and chemicals.
In addition to bag-making and closing, we offer automated bagging systems, such as the PBC series, which ensure efficient filling, weighing, and sealing processes. Our heat sealers, like the NLI-6000, provide secure closures for various materials, including plastic and woven fabric bags. For agricultural products and animal feed, our DS-9C and NP-7A bag closers offer durable stitching, while our fully automated PBC bagging systems are ideal for large-scale operations in the food, chemicals, and construction industries. With decades of expertise, we continue to innovate and deliver reliable, high-performance packaging solutions tailored to diverse industry needs.
Choosing the right paper bag making machine
Selecting the right paper bag making machine involves understanding manufacturing processes, evaluating key features, and considering industry applications. Modern machines offer enhanced productivity through advanced parameters and database management. From clothing to industrial applications, paper bags serve diverse sectors. This section explores crucial factors in choosing a machine that aligns with specific production needs and pump requirements.
Understanding different manufacturing processes
Paper bag manufacturing processes vary depending on production needs and energy efficiency requirements. In Hyderabad, innovative companies utilize conveyor belt systems to streamline production, particularly for e-commerce paper bags. These energy-efficient machines incorporate advanced features like adjustable cutting mechanisms and multi-layer forming units. Understanding these processes helps businesses select the most suitable equipment for their specific applications:
- Flat bag production for retail and food service
- Twisted handle bag manufacturing for boutique stores
- Square-bottom bag creation for industrial packaging
- Multi-wall bag fabrication for heavy-duty applications
- Window bag production for product visibility
Key features of modern paper bag making machines
Modern paper bag making machines incorporate advanced features for efficient production and deployment. These systems often include integrated heat sealer machines for secure closures and heavy-duty bag closing mechanisms for durability. Precise measurement capabilities ensure consistent bag sizes, while automated packing systems streamline the production process. Companies can select machines with adjustable settings to accommodate various bag types and sizes, optimizing versatility for diverse packaging needs.
Real-world applications of automatic bagging machines
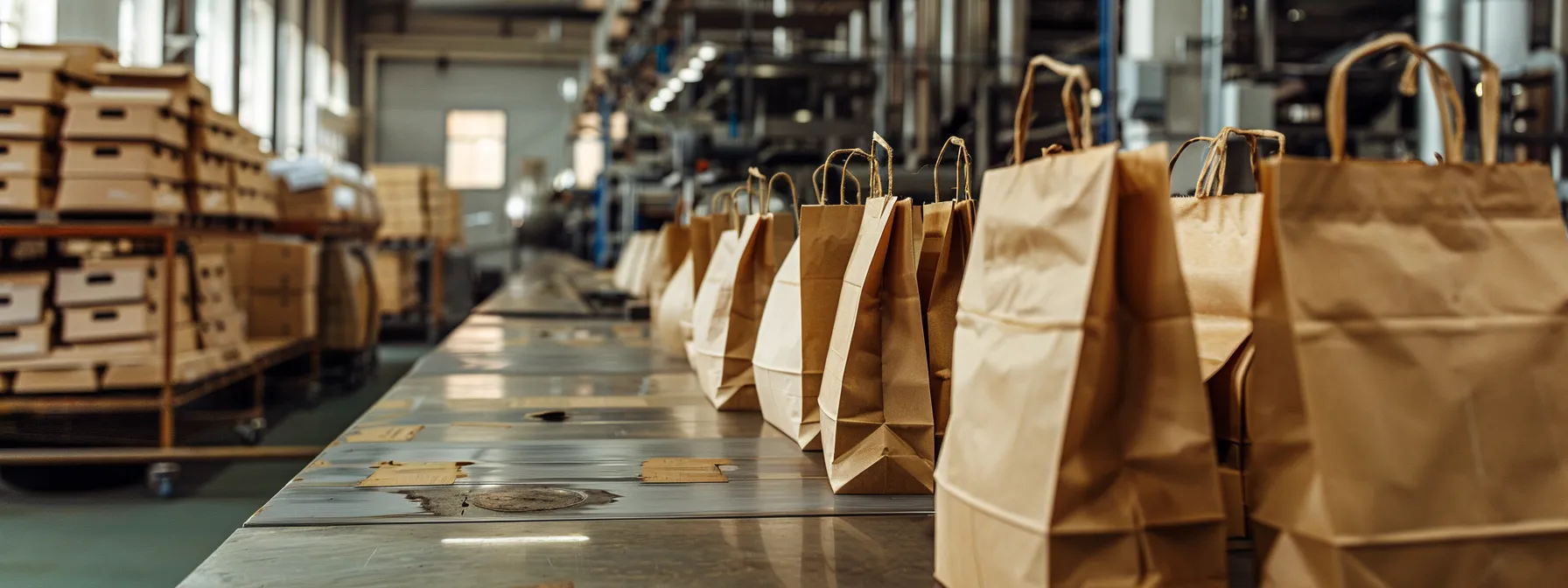
Automatic bagging machines revolutionize packaging across industries. In food production, these systems ensure precise portioning and hygiene. Pharmaceutical companies rely on them for sterile packaging and accurate dosing. E-commerce fulfillment centers use bagging machines to streamline order processing. Advanced engineering, including SCADA systems and touchscreens, enhances communication and control. From raw material handling to final sewing, these machines optimize efficiency throughout the packaging process.
Case studies in food industry packaging
Automatic bagging machines have revolutionized food industry packaging, as evidenced by several case studies. A leading snack manufacturer implemented a sheet-fed machine equipped with advanced robotics and energy management systems, resulting in a 30% increase in production efficiency. The machine’s integrated dashboard provided real-time data on packaging metrics, enabling operators to optimize processes and reduce waste. Another case study from a cereal company showcased the use of bubble wrap dispensers in conjunction with bagging machines, enhancing product protection during transit:
Packaging solutions for the pharmaceutical sector
Automatic bagging machines also offer innovative packaging solutions for the pharmaceutical sector, addressing stringent requirements for sterility and precision. These systems incorporate features like biodegradable bag options and mouth-sealing technologies to ensure product integrity. Advanced machines utilize cache memory for efficient operation and can handle various materials, including paper and animal-derived components. The pharmaceutical industry benefits from these machines’ ability to maintain a controlled environment, which is crucial for sensitive medications:
- Sterile packaging capabilities for medications
- Precise dosage control for powders and liquids
- Integration with cleanroom environments
- Traceability features for regulatory compliance
- Adaptability for various pharmaceutical packaging formats
Future trends in automatic bagging technology

Future trends in automatic bagging technology focus on sustainable packaging solutions and increased automation in production lines. Research in the United States and globally is driving innovations that optimize machine tool efficiency and increase packaging volume. These advancements address environmental concerns while enhancing productivity, as detailed in industry PDFs and publications.
Innovations in sustainable packaging solutions are transforming automatic bagging machines to meet environmental demands. Manufacturers are incorporating sensors and touch screens to optimize material usage and reduce waste. Advanced systems now feature augmented reality interfaces for enhanced operator training and troubleshooting, improving overall uptime. These machines efficiently handle various products, including flour, while minimizing environmental impact. The integration of biodegradable materials and energy-efficient components marks a significant shift towards eco-friendly packaging processes:
Frequently Asked Questions
What are the main functions of automatic bagging machines?
Automatic bagging machines streamline packaging processes by weighing, filling, sealing, and labeling bags with precision. They enhance efficiency, reduce labor costs, and ensure consistent product quality across various industries, from food processing to industrial materials handling.
How do I choose the right paper bag making machine?
Choosing the right paper bag making machine depends on your production needs, budget, and available space. Consider factors like bag size and style, production speed, material compatibility, automation level, and machine quality. Feel free to contact us to find a solution that aligns with your requirements.
What types of automatic bagging machines are available?
Automatic bagging machines come in various types, including vertical form-fill-seal (VFFS), horizontal form-fill-seal (HFFS), open-mouth baggers, valve baggers, and robotic bagging systems. These machines cater to different product sizes, packaging materials, and production speeds, offering solutions for diverse industry needs. Take a look at our engineering units to find more information about each type of bagging machine.
What maintenance is required for packaging machines?
Regular maintenance for packaging machines includes cleaning, lubricating moving parts, inspecting seals and belts, calibrating sensors, and replacing worn components. Adhering to manufacturer-recommended maintenance schedules and conducting routine checks ensures optimal performance, reduces downtime, and extends machine longevity.
What are the key factors to consider when selecting a bagging machine?
When selecting a bagging machine, consider the product type, desired packaging material, production speed, accuracy requirements, and available space. Evaluate automation levels, ease of maintenance, and compatibility with existing systems. Assess the machine’s flexibility to handle different bag sizes and shapes, ensuring it meets your production needs and budget constraints.
Conclusion
Selecting the right automatic bagging machine is crucial for optimizing production efficiency and meeting specific industry requirements. These advanced systems offer significant benefits, including enhanced throughput, reduced labor costs, improved packaging consistency, and environmental sustainability. Businesses can choose machines that align with their operational goals and future growth projections by carefully evaluating production volume, bag types, and automation levels. Investing in the appropriate automatic bagging technology streamlines packaging processes and positions companies for long-term success in an increasingly competitive market.